Maybe I should have come here first before getting my hands dirty, but I did free the worm from the output shaft of the motor. It took about 10 minutes of continuous heat to the motor and some additional flux and solder (what I'd assume to get the other solder to flow) and a quick blow from a pliers straddling the shaft popped it right off.tyler I have used the original shaft from old locomotive motors , I use JB quick to strengthen the joint between the front plate and the bottom plate, then remove the top plate , and the back plate. I usually retain the back plate, re shape it and add it to the front plate for more bearing surface (not needed in this example). then I can cut and pry the armature pieces and commutator off the shaft. trim the shaft and install a smaller, more efficient can motor, using the remainder of the original motor as a base; and using a shaft connector, retaining the business end of the original shaft, and the original worm.
View attachment 146770
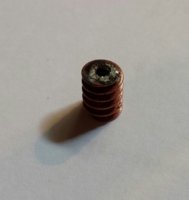
Since I had the iron hot I soldered up my connector that I bought and received last night. Looks like I need to sharpen up my small soldering skills a bit, but all connections are separate with no solder bridges. I'm excited to get this installed into #44's tender as its been forever since I've last installed a sound decoder, let alone a steamer. Eventually the wires will be painted to camouflage them.
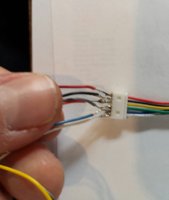