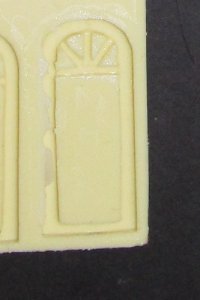
I have two molds ready. the roof arch and round window mold has a small tear. It has some deep undercuts, and If I were aiming at 100 % perfection I would re do it with high strength RTV compound.
but if I was aiming at 100 % perfection I wouldn't have used the roof arch master as it is, as it is slightly lopsided.
I have these molds ready to go, so my next step is to try to estimate the volume of the molds. I'm going to fill them with water,, and then pour the water out, collect it in a measuring cup like the ones that will be used for measuring the casting resin. that way I can get a close estimate of how much resin to mix up so I have enough, but am not wasting much casting resin.
The process from reading the instructions is to warm the mold in the oven or microwave to warm the mold. this will warm the resin as it is poured in the mold, and help it cure. the warmth may also help the resin flow into all the nooks and crannies.
equal amounts of the resin and hardener are mixed together, one is clear and the other is dark, you mix them until no swirls are visible and then pour the stuff in the molds. the resin is supposed to start hardening 90 seconds after mixing, and be hard enough to de mold after 3-7 minutes.
This applies to the Alumilite starter kit, working with other stuff, read the instructions.
In the detail photo of the window, you can see a flap of mold material that crept between the backing plate and the window master. this doesn't exist any more, as I used a rail nipper to remove it.
sadly , with a 90 second work time with the resin there will not be a photo of the resin pour, as I will have only 90 seconds and two hands.
once I have the first of the window and door castings, I can do the final plotting of the window and door locations, cut out the holes, and do some of the inside and outside painting of the structure , which will be needed to give the model a solid look, and more importantly help prevent warping of the foam core.
This is going to be fun!