Hi all
More update.
Started with digging arms assembly
First I joined the Arm 1 (I.e. the boom) with its hinges. Then I glued in the hinge and the axle for the boom to stick hydro actuator with the actuator
Then came the Arm 2 (I.e. the stick) with its hinges.
Afterwards the hinges and the side cheeks for stick to bucket actuator with the actuator were installed.
Then the bucket was installed on its axle, followed by connecting arms for the bucket.
I must mention that almost all axles had to be remade from scratch. As I noticed earlier, I used thicker paper than suggested by designers. I also laminated some parts with 0.6-0.8 mm cardboard to make them look in scale. This brought to some axles being too short or too long. Also hinges 2 and 7 became too wide and had to be cut in two and narrowed by removing 2 mm strip from the middle.
Then i tried to dry-fit the parts only to realise that the hydraulic actuators were mixed between. The actuator 3, the long one should be on the boom moving the stick and the actuator 4 should be mounted on the stick moving the bucket.
Removed the hinges 2 and 7, axles, actuators and reinstalled everything in the right way.
Finished assembly by connecting all the bucket linkages, axles and hinges and then mounted the stick on the boom.
Then I connected the main actuators numbered 1 and 2 to their upper hinges
I must say that although the instructions are really clear explaining the sequence of assembly, need to be careful with numbering of the parts and axles. Need to understand exactly what is done now. Nothing too hard for builder with some experience
Sme pictures below
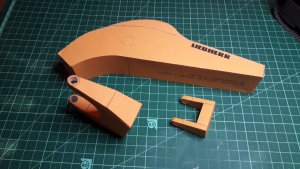
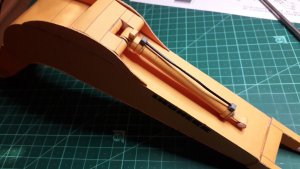
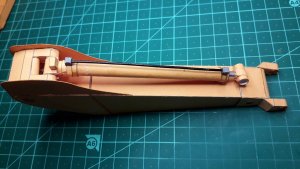
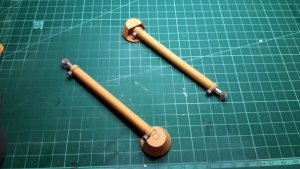
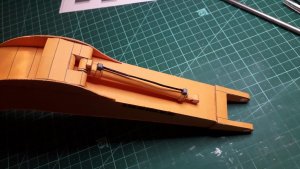
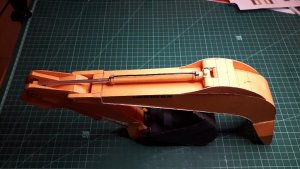
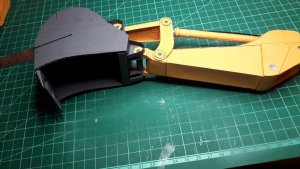
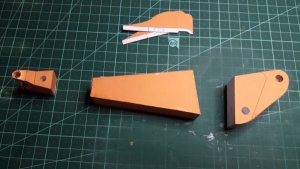
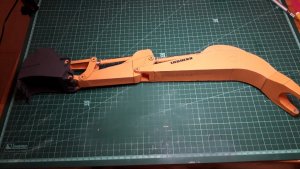
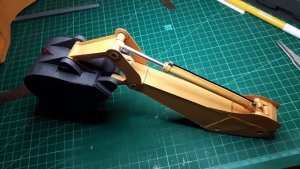
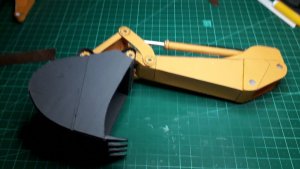
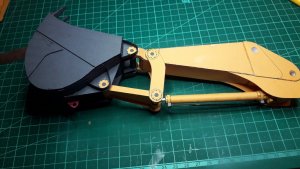
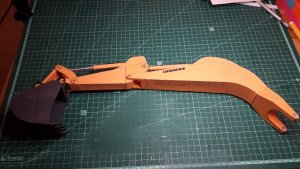