- Apr 5, 2013
- 13,498
- 9,549
- 228
I fired up and printed out my 1st Benchy on my Creality K1 Max, in PLA. Total elapsed time was 15 minutes. One minute less than was stated. It came out great. I have printed out 2 cell phone holders I got off of "Thingverse". I learned a good lesson, don't print anything that is against that table and has a ripple edge. Lots of flashing clean up required. Not really hard, just tedious.
I'm getting a new keyboard, this one works great but the letters are rubbing off, and it's filthy.

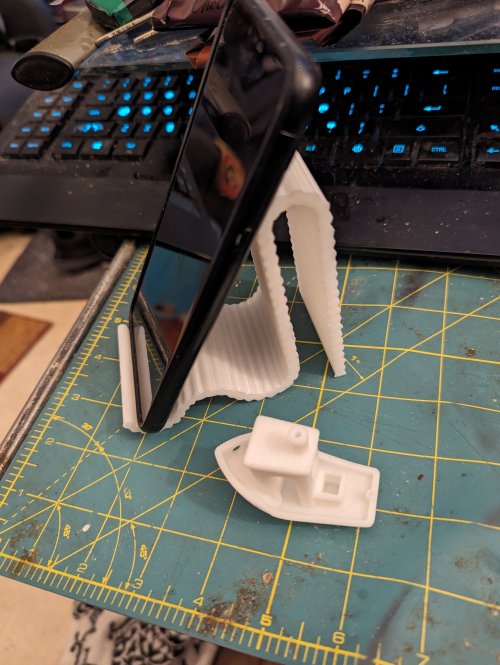
I'm getting a new keyboard, this one works great but the letters are rubbing off, and it's filthy.
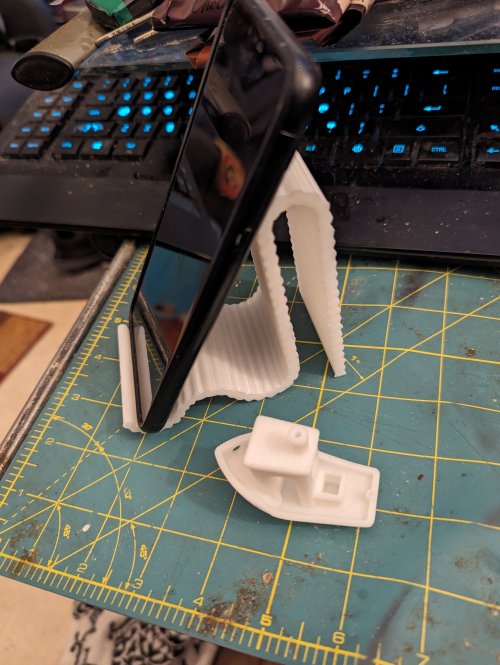