Gogsnik said:
A very professional looking build, carefully executed. I always have problems cutting plasticard strait but this whole build looks as neat as a pin.
I've been asked so often how I cut Plasticard and fabricate my models I've made a stock answer:
How are you getting such clean cut lines when you cut the plasticard?
Ah, that is the question I am asked most often and the answer cannot be repeated too many times because I think it the singular most important ability to achieve when anyone sets out to scratch build.
Regarding tools I don't use anything special. Aside from what you see here I do have a Dremel cordless, a cheap electric scroll saw, and a desk top belt sander all of which are rarely used.
The main cutting tool I use is the retractable blade Stanley utility knife and I do have a see through plastic 12 inch scale to take measurements off of my LCD monitor.
I have two computer programs that allow me to scale the images and magnify them; ACDSee 14 and ULead Photo Impact 13 Editor.
The biggest problem new scratchers have is using the wrong cutting tool. Craft cutting tools such as Xacto knives are useful and I have two pictured above, these are for fine detail work not for basic cutting and shaping.
As stated previously the Stanley Utility knife is the single most important tool in your inventory; it doesn't have to be of that manufacturer but of this type.
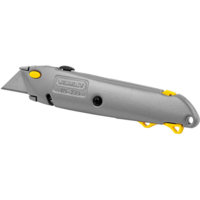
Small plastic handle snap off blade retractable knives of the type shown below are useless for hobby work, the blade
wobbles in the grip and you are more likely to injure yourself than to do any decent cutting with a tool of this type
In addition you will probably require:
A steel straight edge, sanding blocks (coarse and medium grit), and single cut 'farmers' file are used to get straight clean cuts and crisp 90° edges. You'll never get that with a 1/4 inch Xacto knife.
Another trick is score and snap; using the utility knife and straight edge score a line on the sheet plastic then a second to deepen the cut ( make additional passes for thicker sheets) then snap the sheet at the score line.
Always make two or more shallow cuts instead of trying to cut through with a single pass.
Dress your edges with the file and sanding blocks.
This should get you started, please ask for any clarification on the above.
As for detail, its hard to explain but my feeling is "More is better." A good supply of scrap styrene and bitz is essential and just try to duplicate what you see. Practice is the catch word here, there is no shortcut to experience and I am still learning myself.
Regarding the clothes pins I reverse the wood jaws in the spring for better clamping and I do have quite a few likewise with the modeling bar clamps. They are cheap here, I don't know if they are in New Guinea but you can order them on line from Amazon or Harbor Freight for about $2 bucks each:
I hope this helps but if not feel free to ask about anything that is unclear.