"Men do cry, but only when assembling furniture." ~ Rita Rudner
I got so excited about getting to this stage of completing the main hull, that I completely forgot to take pics of the final assembly of the rear hull.
There is nothing difficult here, just follow the instructions. Just make sure everything is square and true when gluing.
The joints between each sub-assembly needs to be as tight as possible, without gaps. I compressed mine together to the limits of structural collapse to achieve this!!
If there is too much spacing between the sub-assemblies, the ends of the rear detail panels will protrude too far over the edge of the lateral spine....
I just had to place the rear hull construction, unglued, onto the lateral spine, just to see what it looks like!!
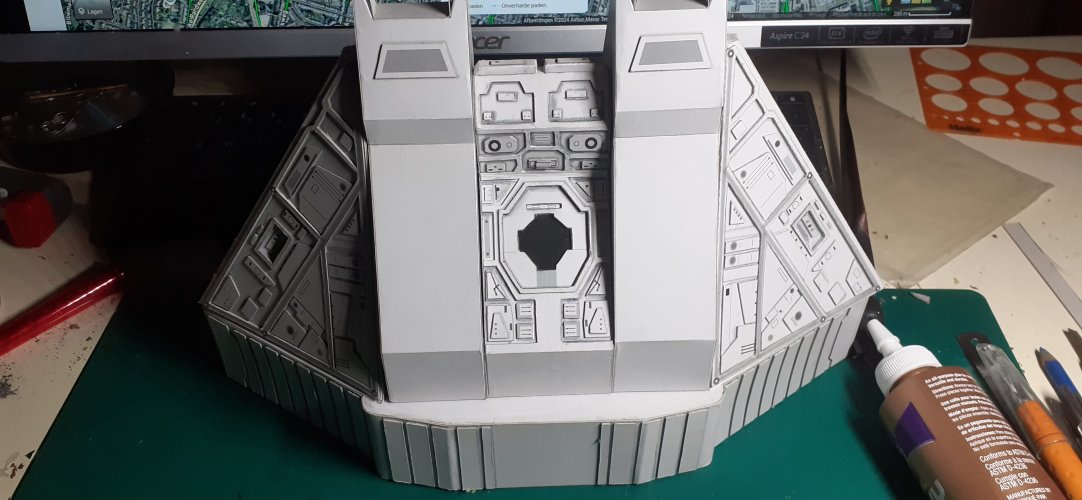
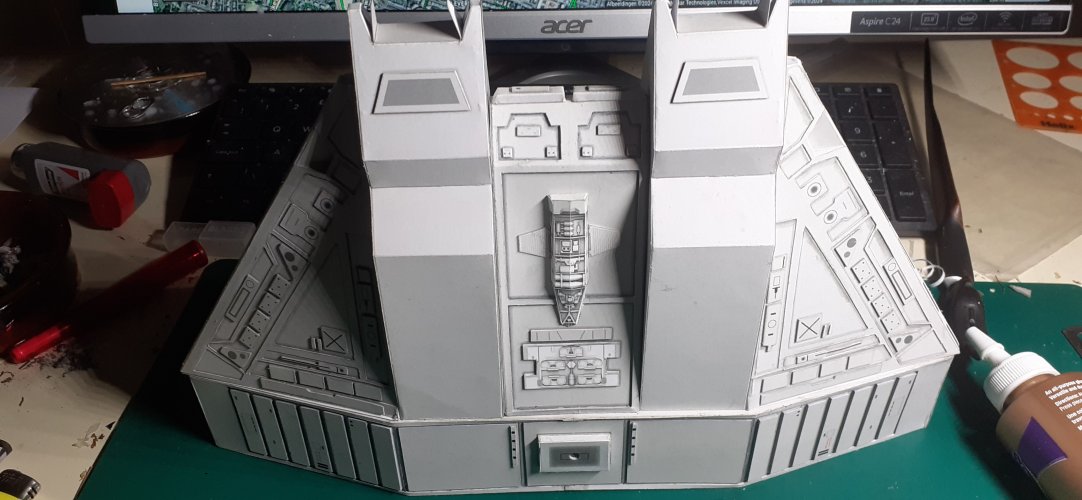
And, well, me being me, with good balancing abilities, I had to go one step further........ (The proverbial beer can is 17cm high, btw.)
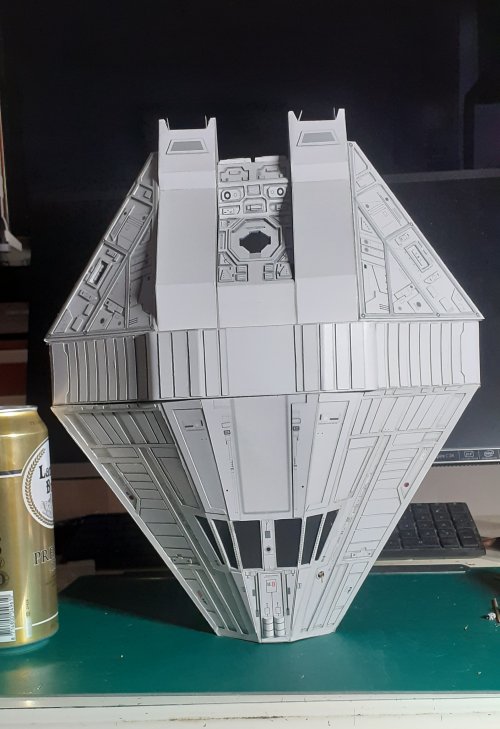
But, then I noticed a few problems like this..... Some parts had pulled away, causing the parts to not join correctly. In this case, the forward hull and the lateral spine.
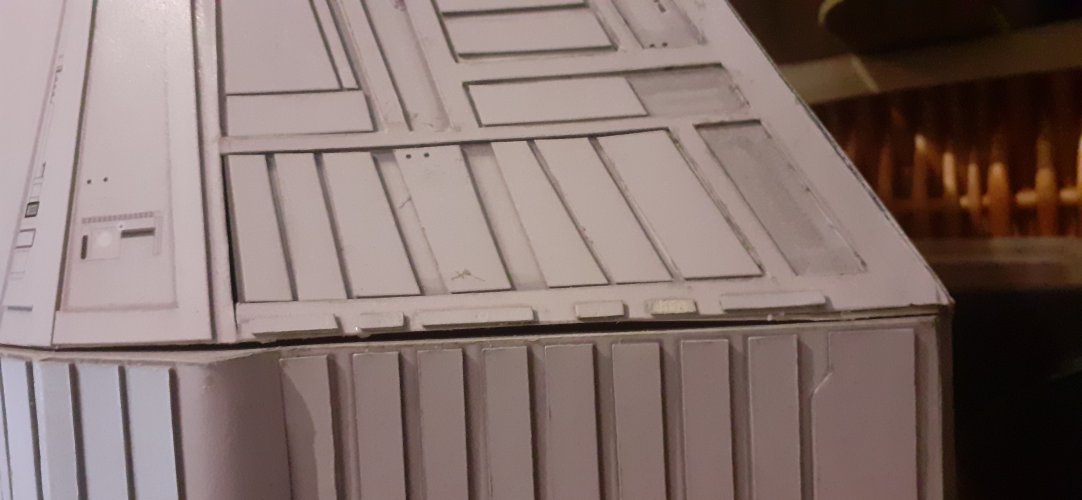
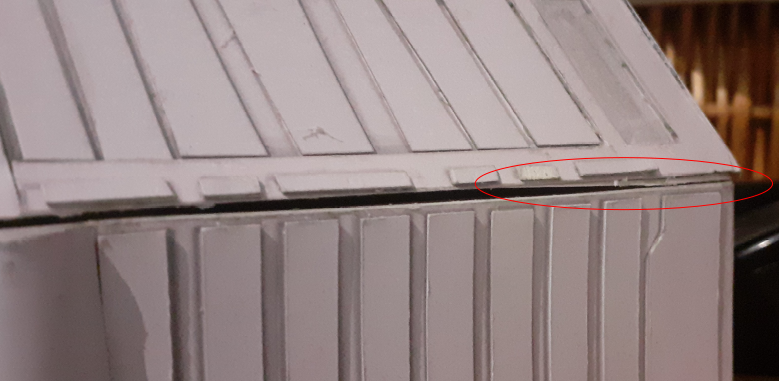
Time for repairs before I go any further with the build.....
Back soon with more ,when the repairs are done....

I got so excited about getting to this stage of completing the main hull, that I completely forgot to take pics of the final assembly of the rear hull.

There is nothing difficult here, just follow the instructions. Just make sure everything is square and true when gluing.
The joints between each sub-assembly needs to be as tight as possible, without gaps. I compressed mine together to the limits of structural collapse to achieve this!!
If there is too much spacing between the sub-assemblies, the ends of the rear detail panels will protrude too far over the edge of the lateral spine....
I just had to place the rear hull construction, unglued, onto the lateral spine, just to see what it looks like!!
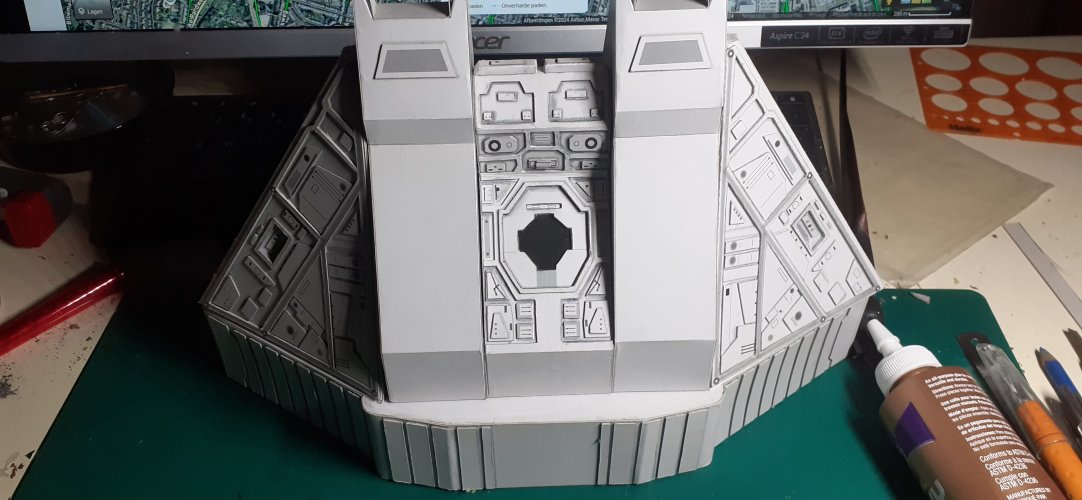
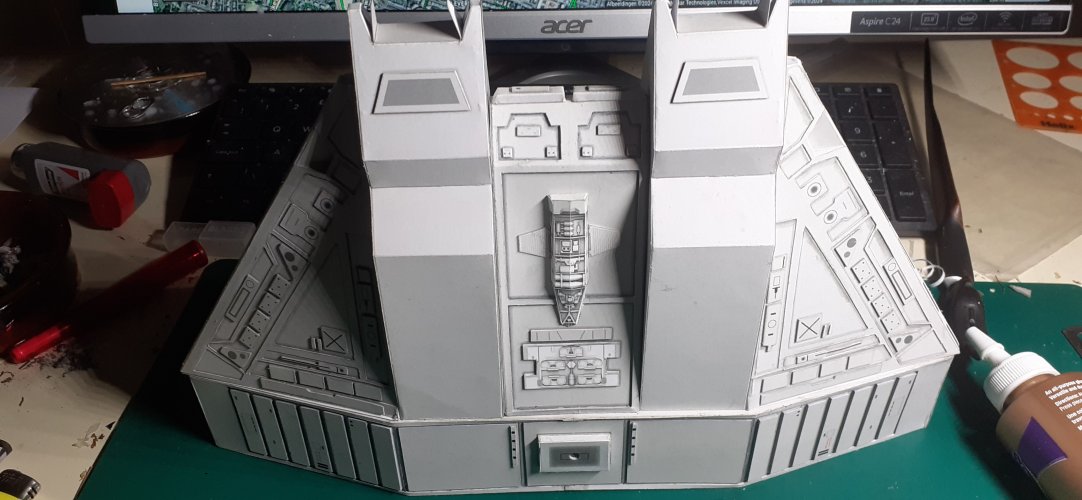
And, well, me being me, with good balancing abilities, I had to go one step further........ (The proverbial beer can is 17cm high, btw.)
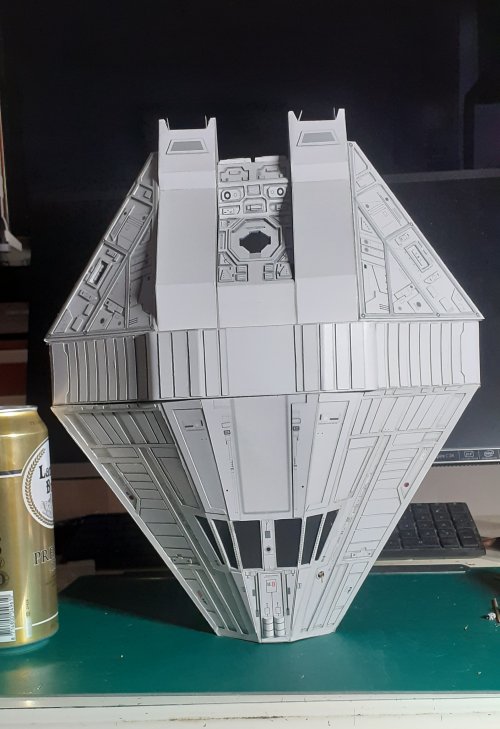
But, then I noticed a few problems like this..... Some parts had pulled away, causing the parts to not join correctly. In this case, the forward hull and the lateral spine.
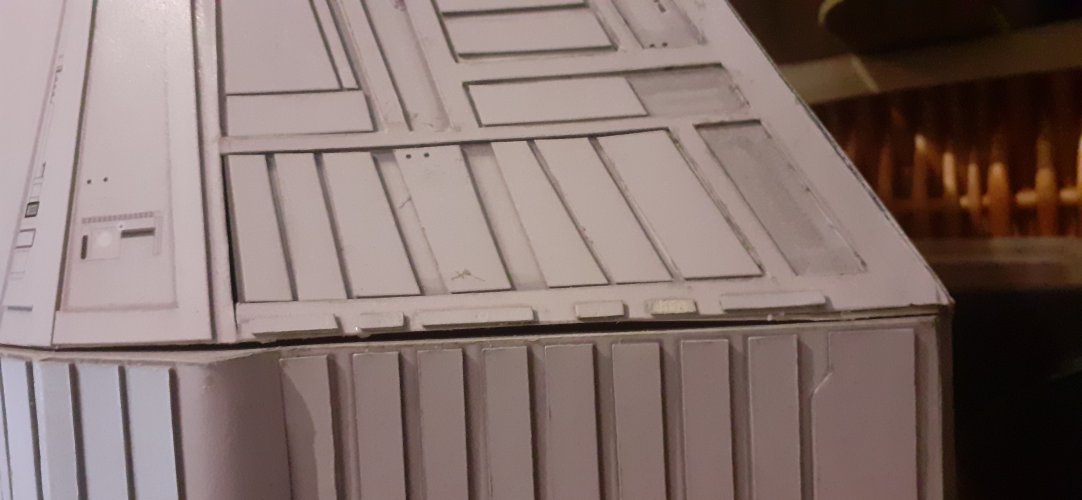
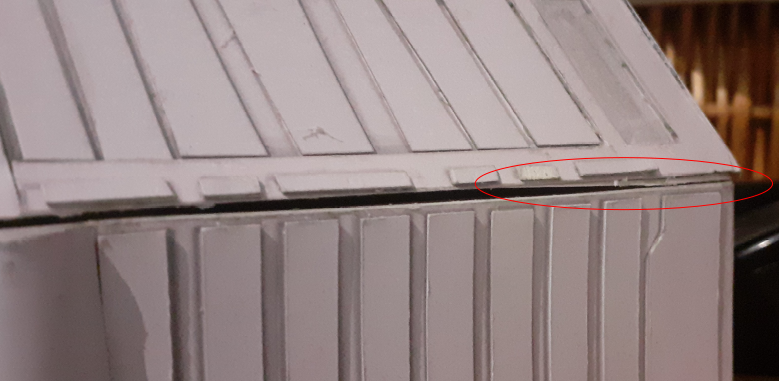
Time for repairs before I go any further with the build.....

Back soon with more ,when the repairs are done....

Last edited: